Boilers
WTE has a long experience in the design of boilers and can engineer superheated steam, superheated water, and diathermic oil boilers.
Over the years we have developed and applied original solutions, striving for efficiency and reliability.
Our boilers are designed to supply superheated steam at a temperature up to 500 ยฑ5 ยฐC, and a pressure up to 80 bar.
Specializing in the processing of municipal solid waste and other “difficult” fuels, we have a distinctive experience in the design of boilers recovering heat from fumes containing aggressive chemicals, or abrasive because of their high amount of dust.
Modeling and Simulation of Boiler Behaviour
Design options are carefully evaluated through detailed modeling of the boilers. This activity allows for a correct thermodynamic and mechanic dimensioning of the boiler.
This model investigates, among other things:
- heat exchanged with the combustion section
- fouling (especially the differential fouling of exchange surfaces) and ashes accumulation
- areas potentially subject to corrosion
- tubes surface temperature
The project emerging from these first steps is then validated using Computational Fluid Dynamic model.
Horizontal Boilers
Easier to maintain and less sensitive to problems from dust,ย horizontal boilers are the most common choice in waste incineration plants.
Given our experience in the engineering EfW systems, we are particularly skilled in the design of boilers to be operated in situations where high maintainability is required.
Design Options and Criteria
- The first radiant section has one or more vertical passes, to easy separation and accumulation of coarse dust in the underneath hopper
- Membrane walls can be realized welding together finned or non-finned tubes. The first option is costlier, but has tremendous advantages when the need for replacing some tubes arises, thus being the best choices for particularly demanding applications
- Horizontal convective section, realized withย membrane walls, hosting tube bundles hanging from its ceiling
- Dust in a horizontal fume flow naturally tends to decant, and is collected in hoppers underneath the convective section. While the first tube bundles are more interested by fouling and abrasion due to dust, this is not true for the last onesFor each bundle, the optimal ratio pass/diameter for the tubes is calculated. This allows to eliminate the risk of dust generated occlusions, and to reduce to a minimum the fumes speed
- Speed of fumes is calculated, and the section is dimensioned in order to reduce it to a minimum and minimize abrasion
- The first bundle is an evaporator, in order to protect the next ones from fumes having an excessive temperatureThis section is designed to minimize the temperature of the fumes passing through the superheater bundles, even when tubes surfaces are particularly fouled
- Superheating temperature is defined based on the chemical composition of fumes, and is controlled by a single or double stages attemperation (between the superheater bundles)
- Easy access and inspection to the internal components of the boiler
- Easy extraction of the tube bundles โ if required, we can guarantee that the substitution of convective bundles can be made in 8 hours
- The flexibility of tubes bundles makes possible to clean them mechanically, by percussion of the lower collectors. This avoids the need for installing steam blowers (sootblowers), thus reducing abrasion problems and eliminating the usage of steam, that remains totally available for the production of electric energy in the turbine
Vertical Boilers
Vertical boilers are generally considered less expensive, and they certainly are more compact, occupying less space than the horizontal ones.
But vertical boiler presents two critical issues. The first originates from the need to clean the bundles. The second from the difficulty of the maintenance, especially when it comes to removing the bundles.
For these reasons, when burning waste, RDF or biomass vertical boilers must be designed carefully, starting from an accurate examination of fumes composition and characteristics.
Fouling is generally defined as โthe accumulation of unwanted material on a surface, to the detriment of its functionโ.
As for boilers, fouling is determined by fly ashes accumulation on the leading edges of the bundleโs tubes.
In the specific case of vertical boilers, fly ashes are accumulating at first on the higher bundles. Later they fall down on the lower bundles and eventually collected in the hopper positioned underneath the convective section.
This process is dynamic. In order to understand the behavior of the boiler and the impact of fouling on the performances of the system, we have developed an original predictive model, foreseeing some hypothesis about the degree and the evolution of fouling of the bundles over time.
- A properly dimensioned vertical boiler will have an exchange surface greater than that of a corresponding horizontal, โtail endโ boiler.
- Passes between the horizontal tubes of bundles is over-dimensioned, to allow for the falling of dust and fly ashes
- Installation of soot blowers, to clean the bundles
- Inspection doors are positioned in strategic points, to allow for a constant evaluation of fouling by operatorsย
Slideshow
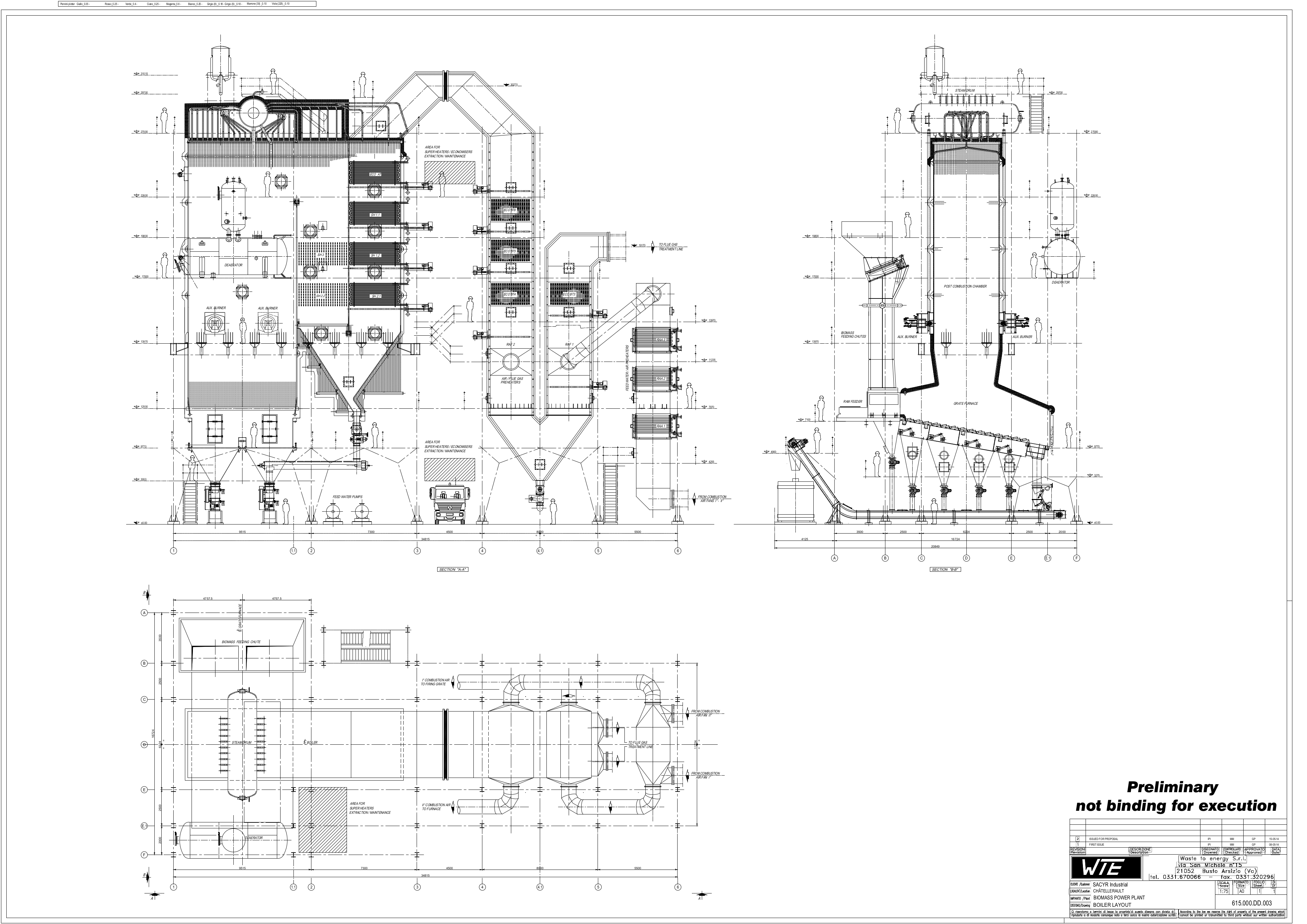
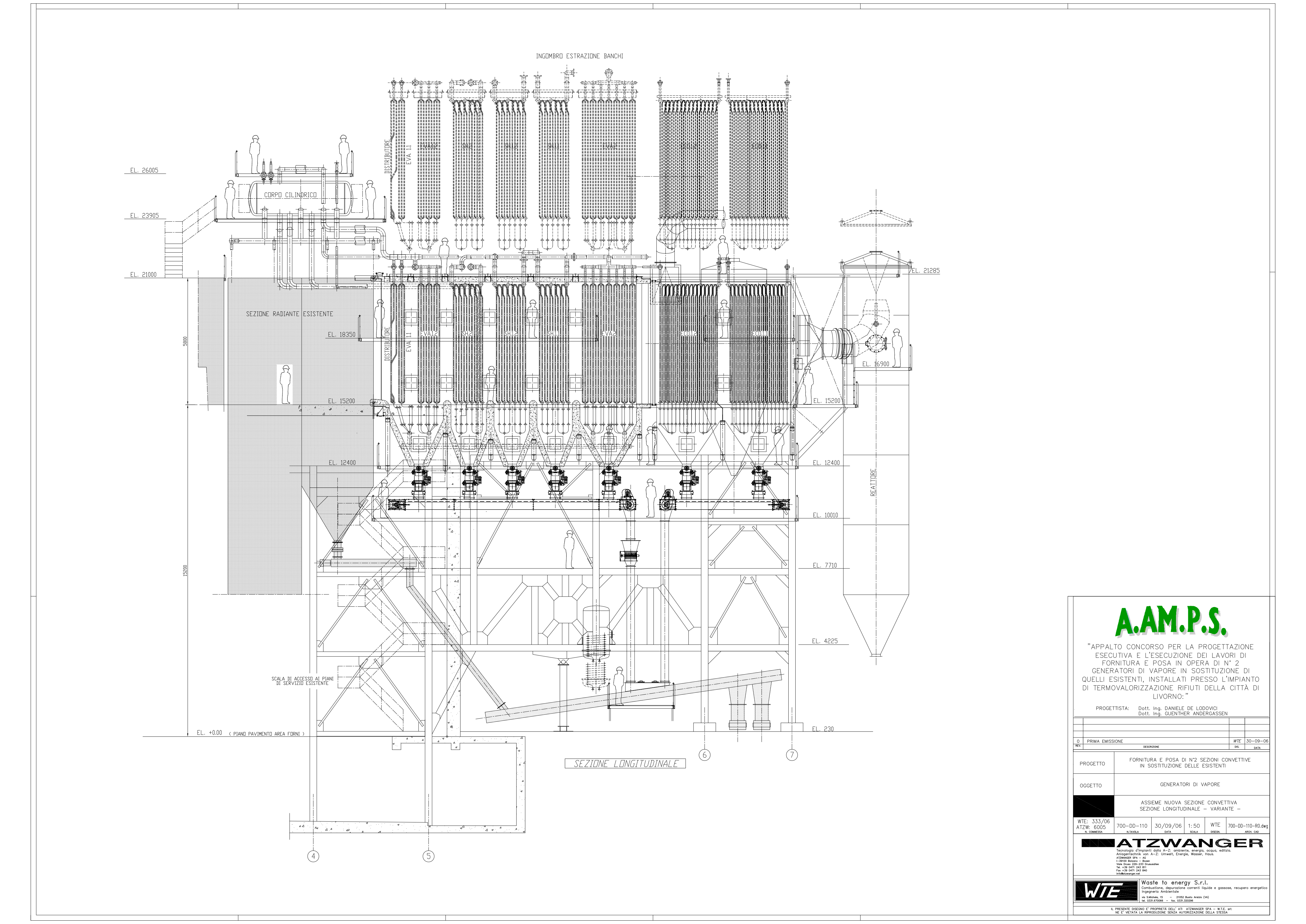
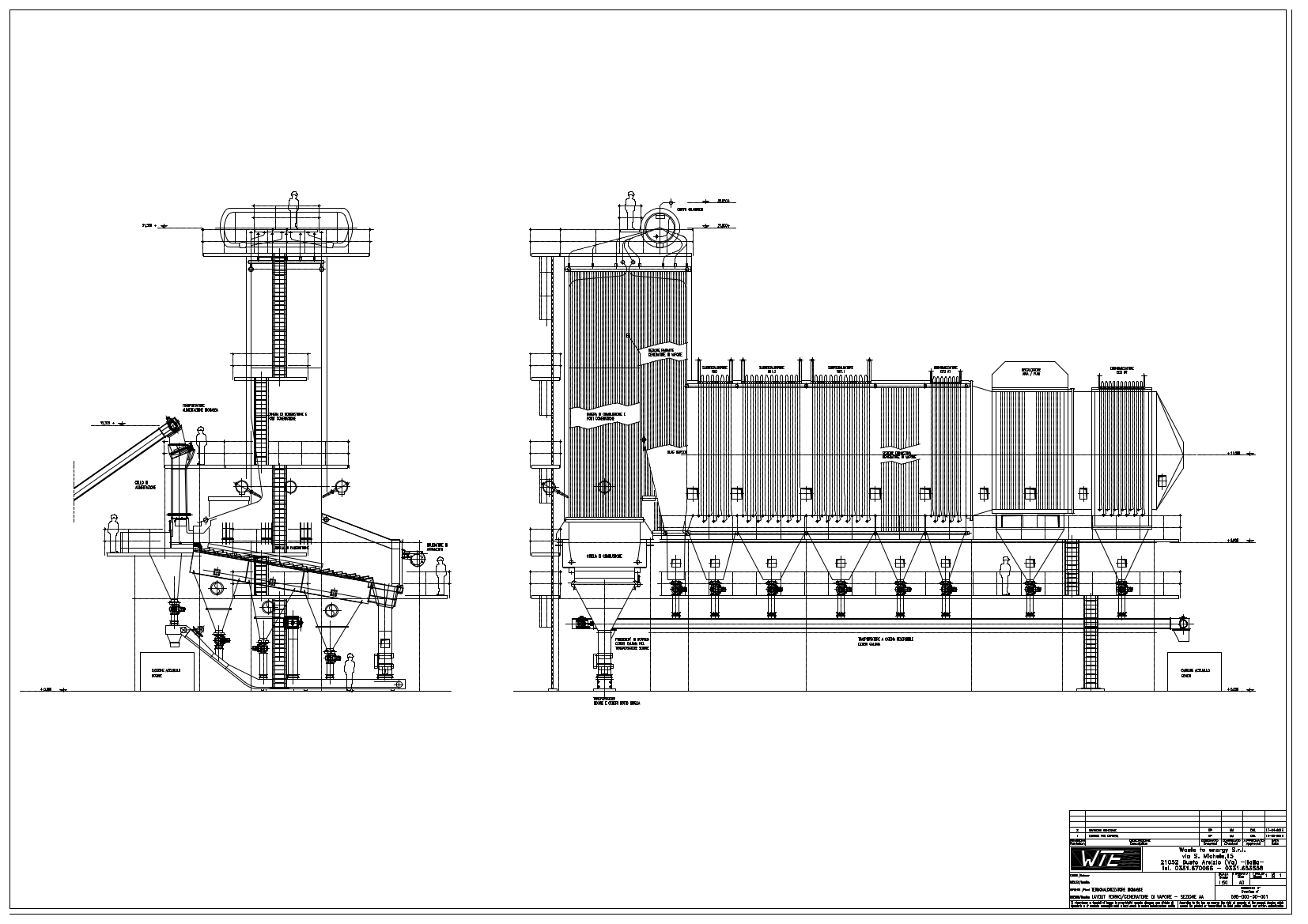
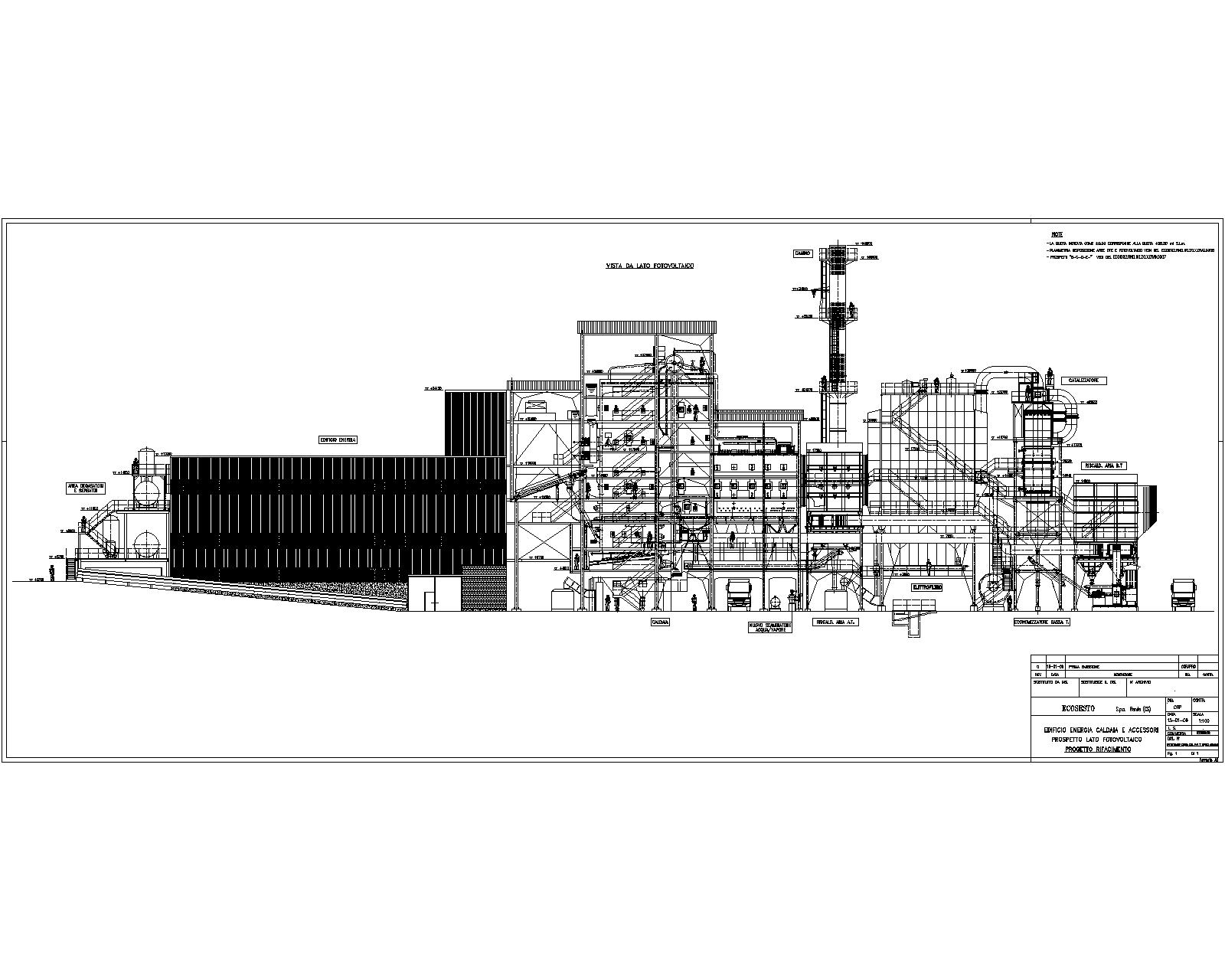
Highlights
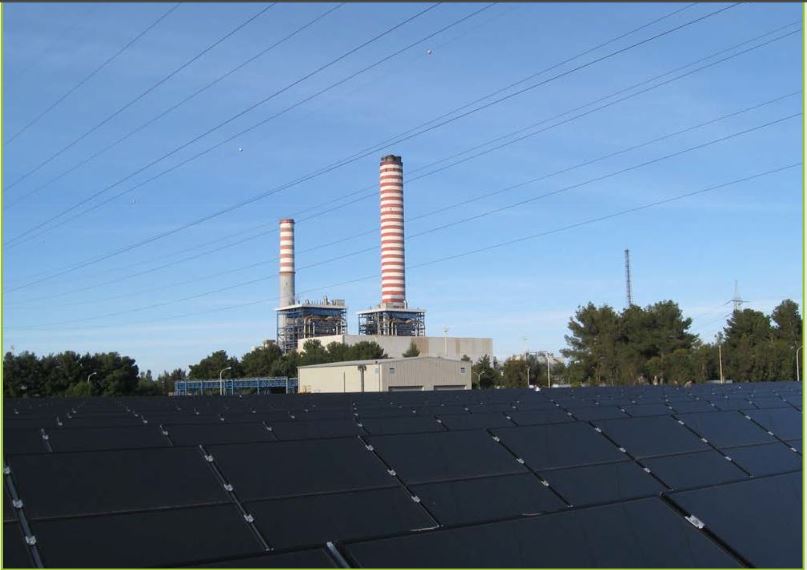
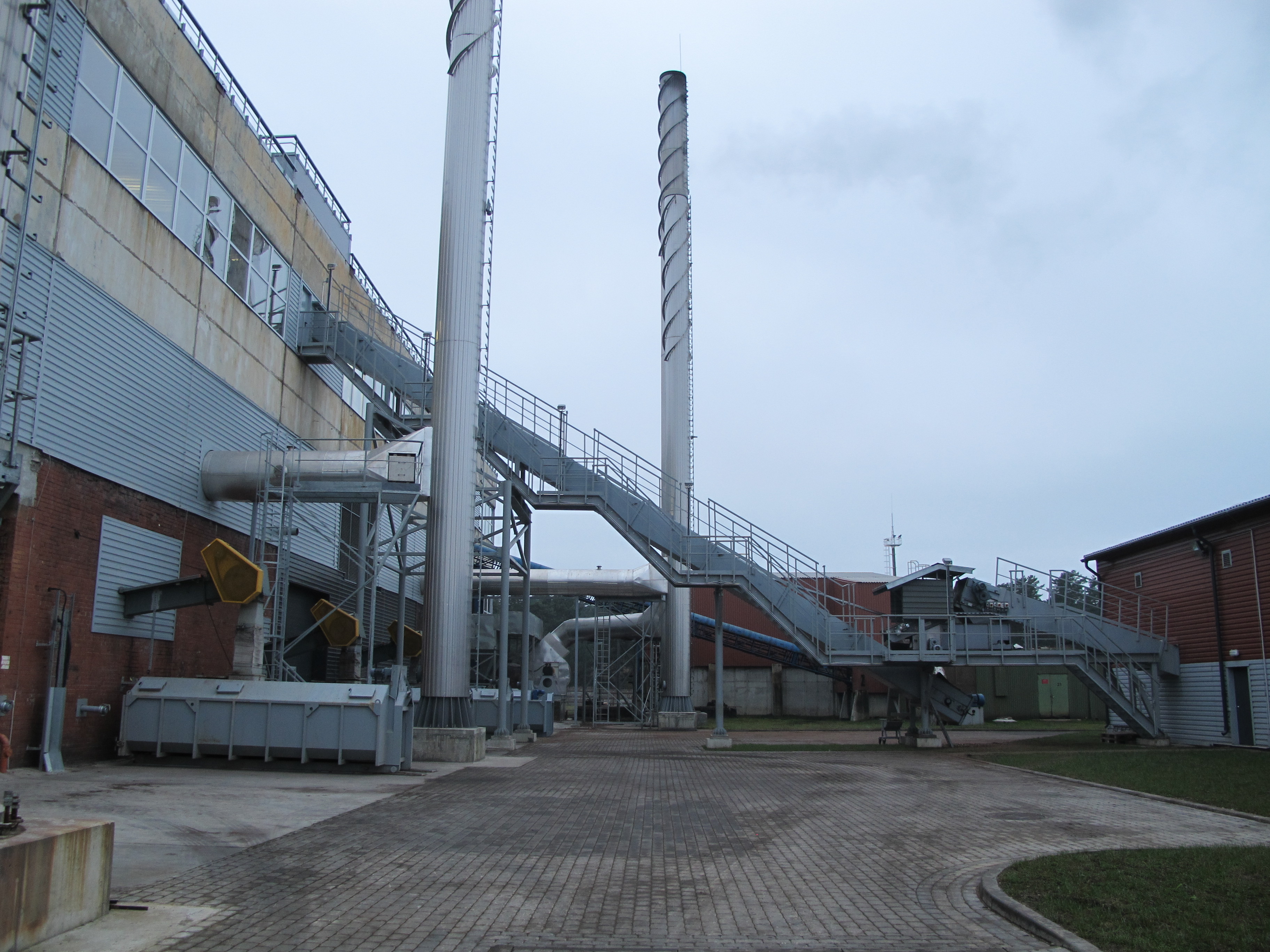
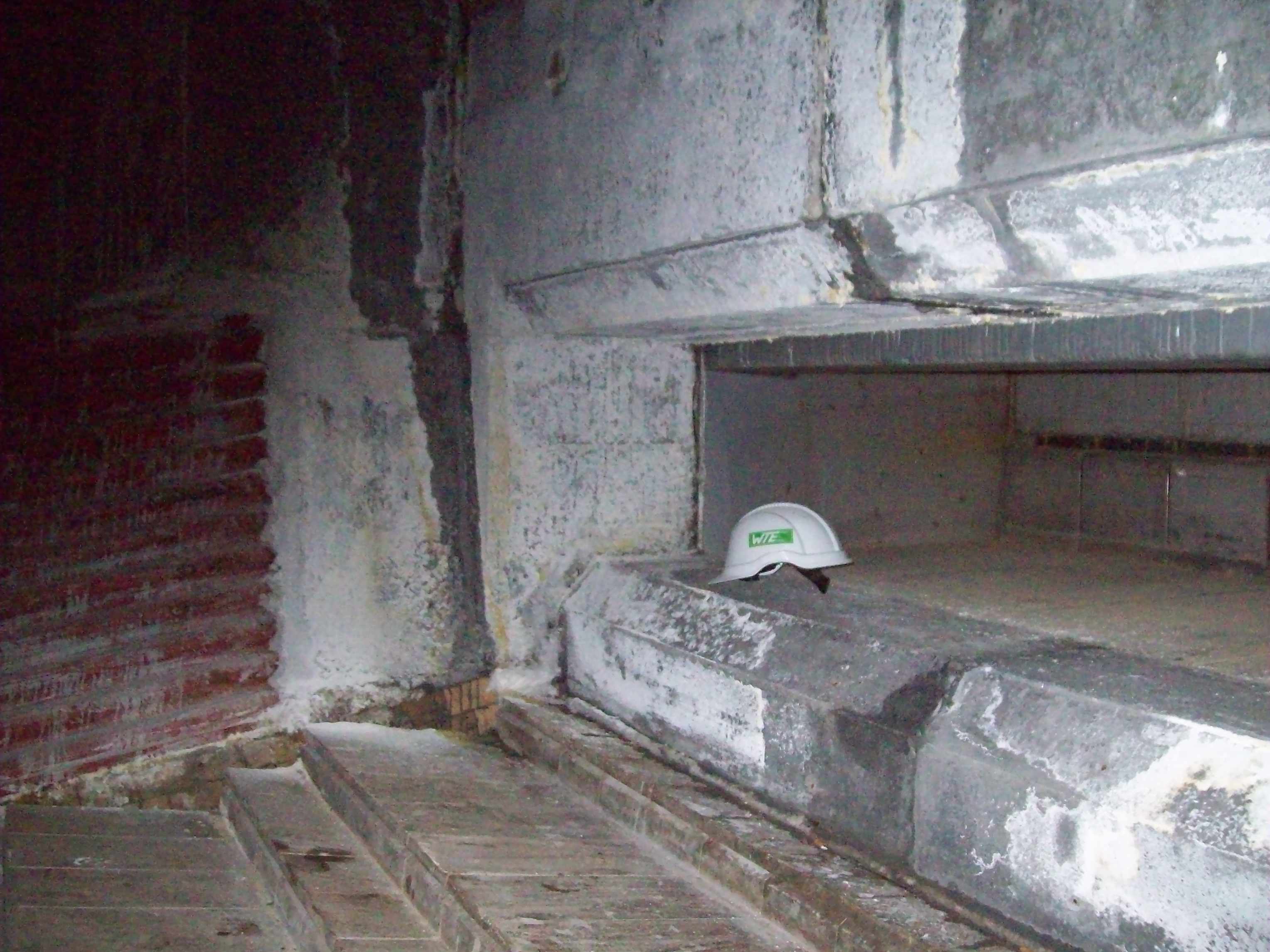
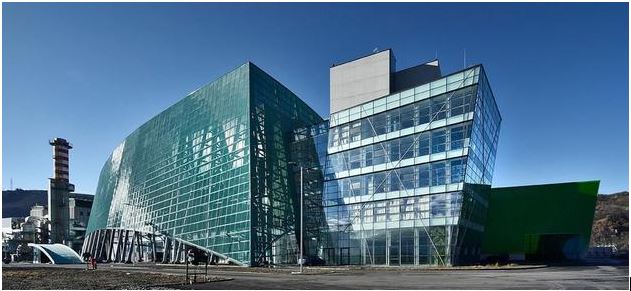
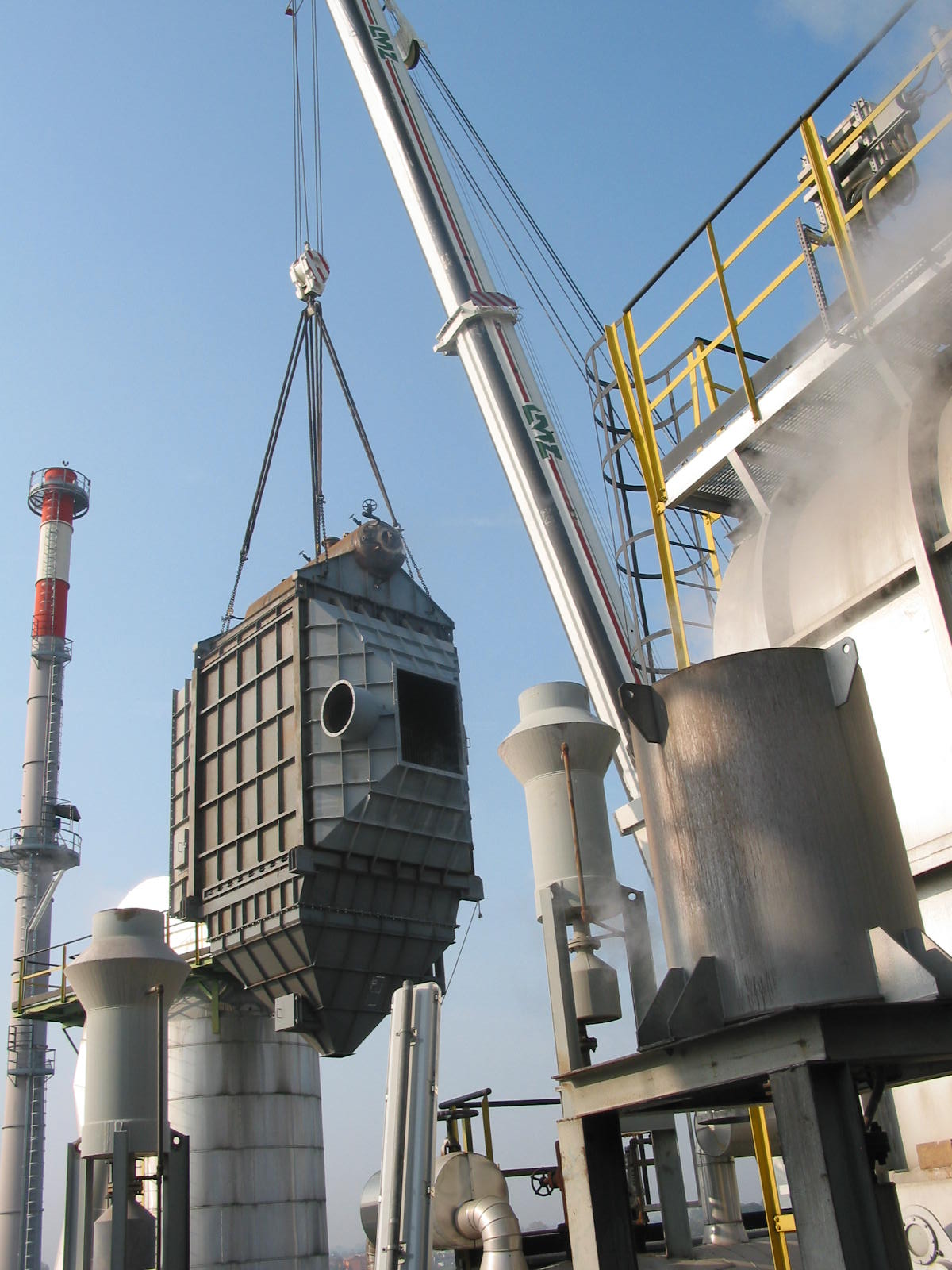
Tell us about your next project
We love facing new challenges, discussing new ideas and envisaging new projects.
Feel free to contact us: we will be glad to exchange opinions, and to figure out how we can be of further help.